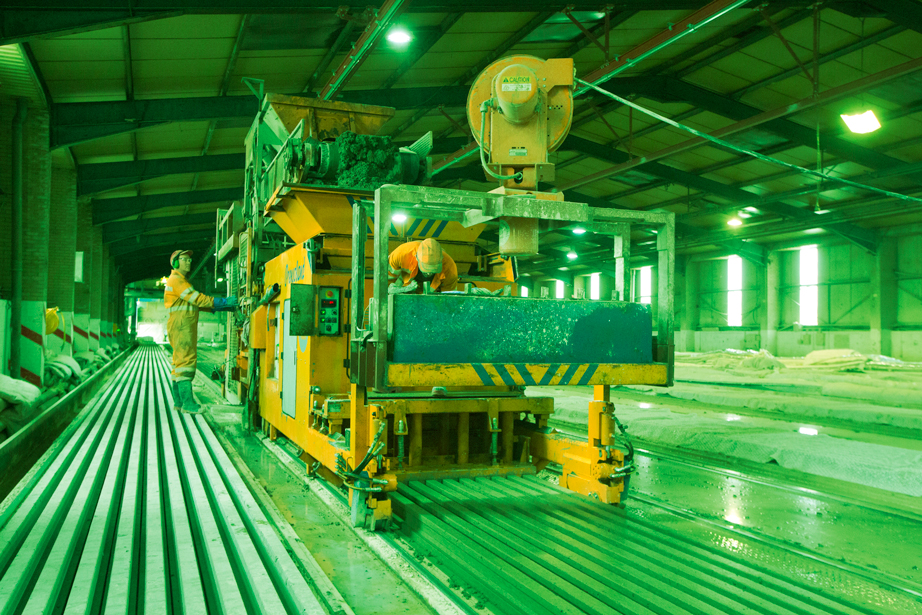
Milbank Concrete Products’ 101 Guide to Precast Concrete
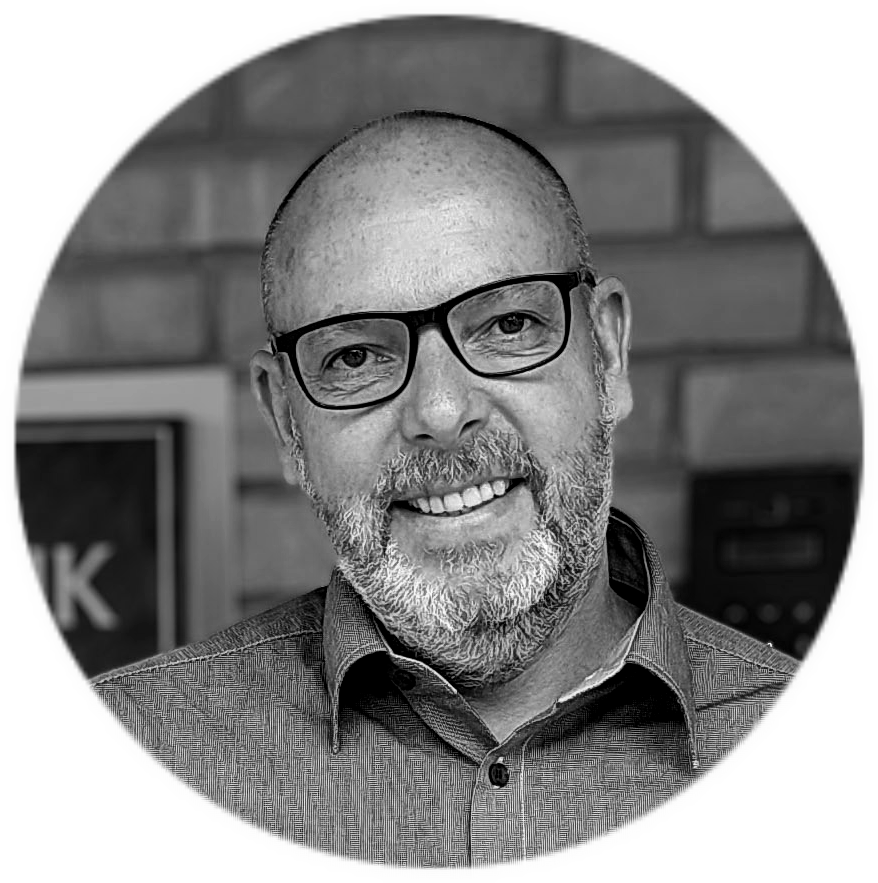
Written by
Lee Cowen, Managing Director
Milbank Concrete Products
04/02/2025
Milbank Concrete Products’ 101 Guide to Precast Concrete
Precast concrete plays a vital role in modern construction, offering a versatile and efficient solution for a wide range of applications.
Most people understand the concept of concrete – after all, it features everywhere in our day to day lives. But what makes precast concrete such a key component in today’s built environment?
As a leading supplier in the industry, Milbank Concrete Products has spent over 75 years perfecting the design, manufacture, and delivery of precast concrete solutions. Most recently we’ve been paving the way to a more sustainable way of working, driving the change in the industry for a better future for our planet.
In this guide, we’ll cover everything you need to know about precast concrete—from its manufacturing process and benefits to its applications and our commitment to sustainability.
What is Precast Concrete?
Traditionally, concrete is often cast in-situ on building sites, being poured into a mould and then left to cure in its final position. However, this can come with its own challenges, including poor weather conditions which mean the concrete won’t cure efficiently.
On the other hand, precast concrete is a construction material produced by casting concrete in a controlled environment, away from the construction site. Once the concrete has set and cured, the finished components are transported to their final destination for installation. This process ensures consistent quality, precise dimensions, customisable designs and improved sustainability in the manufacturing process.
Unlike cast-in-situ concrete, precast elements are made under strict quality control measures, which guarantees a high level of durability and performance. From beam & block and hollowcore planks to stairs and columns, precast concrete offers an unmatched level of versatility.
A Brief History of Precast Concrete
The use of precast concrete dates back to ancient times, where concrete was used to construct impressive structures like the Colosseum and aqueducts.
While the Romans and Ancient Egyptians relied on simple techniques, advancements in technology during the 19th, 20th and 21st centuries revolutionised precast concrete – this is when Milbank Concrete Products was born in 1947. Innovations in materials, production processes, and design software have made precast concrete a cornerstone of modern construction.
How is Precast Concrete Made?
Once our team has taken a customer brief and collated our planning documents, the manufacturing process begins with designing moulds tailored to the specific dimensions and requirements of the project. Once the design is finalised, a concrete mix is prepared using high-quality materials. At Milbank, our mix incorporates cutting-edge cement replacement technology, reducing cement usage by nearly 30% without compromising performance.
After the concrete is poured into moulds, it undergoes a controlled curing process to ensure maximum strength and durability. Once cured, the precast elements are transported to the construction site and installed using cranes or other specialised equipment. This efficient process not only saves time on-site but also ensures consistent quality.
Applications of Precast Concrete
Precast concrete is widely used across various industries due to its versatility. Structural elements such as beam & block, columns, and hollowcore planks form the backbone of many commercial and residential buildings. Architectural features, including balconies, showcase precast concrete’s ability to combine function and aesthetic appeal. Additionally, precast concrete is a go-to solution for utility structures like retaining walls.
In infrastructure, it is used for bridges, tunnels, and railway components, while in residential construction, it enhances efficiency and durability in homes and apartments.
The Advantages of Precast Concrete
One of the standout benefits of precast concrete is its consistency and quality. Produced in a controlled environment, it is less susceptible to weather conditions and other variables that can affect on-site construction. This ensures a higher standard of durability and performance.
Time efficiency is another significant advantage. By manufacturing components off-site, construction projects can proceed faster, as installation time is significantly reduced. Precast concrete also offers cost savings in the long run due to its durability and low maintenance requirements.
From an environmental perspective, Milbank Concrete Products is leading the way in sustainable practices. Our cement replacement technology removes over 2,500 tonnes of CO₂e from our products annually. Furthermore, our operations are powered by renewable energy, including solar panels that generate over 306,000kWh of electricity per year. Combined with our use of HVO biofuel and electricity for delivery vehicles and machinery, we’ve achieved a 69% reduction in CO₂ emissions since 2018.
Challenges and Limitations
While precast concrete offers many benefits, it is not without challenges. Transporting large precast elements can be complex and requires careful planning.
Additionally, the upfront investment in moulds and setup may deter smaller projects. Once cast, precast concrete offers less flexibility for on-site modifications, which means detailed planning from our team at Milbank is crucial.
Precast Concrete vs Cast-in-Situ Concrete
When comparing precast concrete to cast-in-situ alternatives, the advantages of precast are clear. Precast concrete offers superior quality control due to its production in a controlled environment. It is also more time-efficient, as components arrive ready for installation. Cast-in-situ concrete, on the other hand, may allow for greater flexibility in design but is often more labour-intensive and weather-dependent.
Innovations and Trends in Precast Concrete
Sustainability is at the heart of our operations. From transitioning to renewable biofuels to generating our own solar energy, we are committed to reducing our environmental impact. Our goal is to achieve net-zero emissions for our scope 1 and 2 activities by 2030—20 years ahead of government targets.